Quality & safety
From before each donor’s milk is expressed to the moment our products arrive at NICUs throughout the world, we work to ensure the highest quality and safety every step along the way.
Standardised quality and safety from start to finish
From donor to recipient, the entire life cycle of Prolacta’s human milk-based nutritional products follows a standardised production process, including donor qualification; screening and blood testing; shipping; DNA matching; testing; storage and processing; pasteurisation and manufacturing; and final product testing and quality review.
Leading the human milk industry in quality and safety
Hospitals choose Prolacta’s human milk-based nutritional products knowing that they are receiving safe, standardised donor milk products processed under the strictest quality and safety guidelines to protect the health and wellbeing of their most fragile patients.
Lab-tested, DNA-matched donor milk
After their doctor and their child’s paediatrician confirm eligibility and supply of excess milk, each Prolacta donor is carefully screened via blood test and a DNA swab is taken. We were the first company to adopt the safety measure of DNA matching to ensure all milk received comes directly from our carefully screened and vetted donors.
Once the donor milk arrives, we test it for pathogens, viruses, adulterants and the presence of nicotine, marijuana, opiates and other substances of abuse.
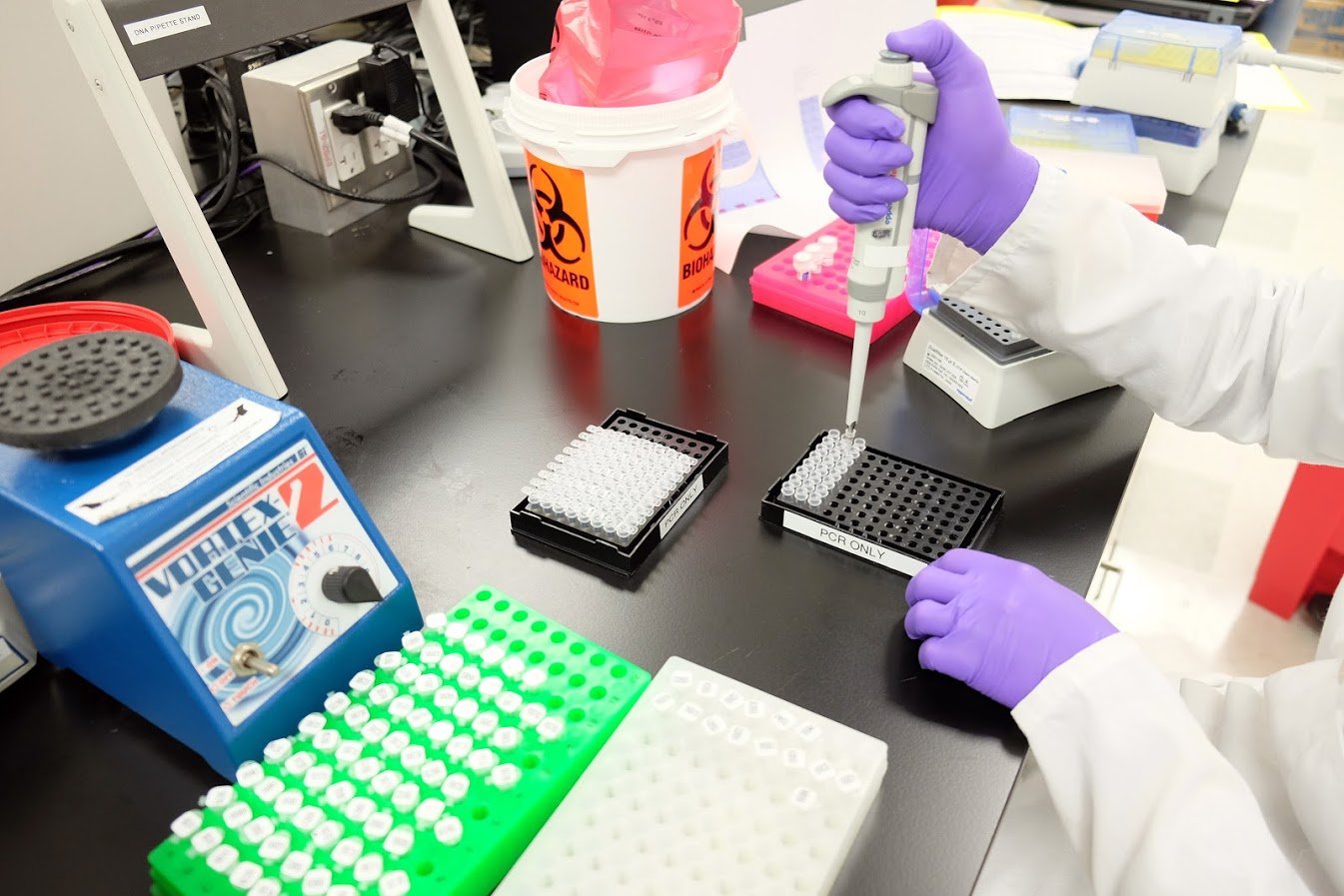
FDA-regulated lab processes
Our human milk safety laboratories and manufacturing processes are regulated by the United States Food and Drug Administration (U.S. FDA).
We operate the first and only pharmaceutical-grade manufacturing facilities for the testing and processing of human milk. Our stringent processes for donor milk screening and testing human milk were modelled on those used in the U.S. plasma and blood industries and surpass food-product safety standards.
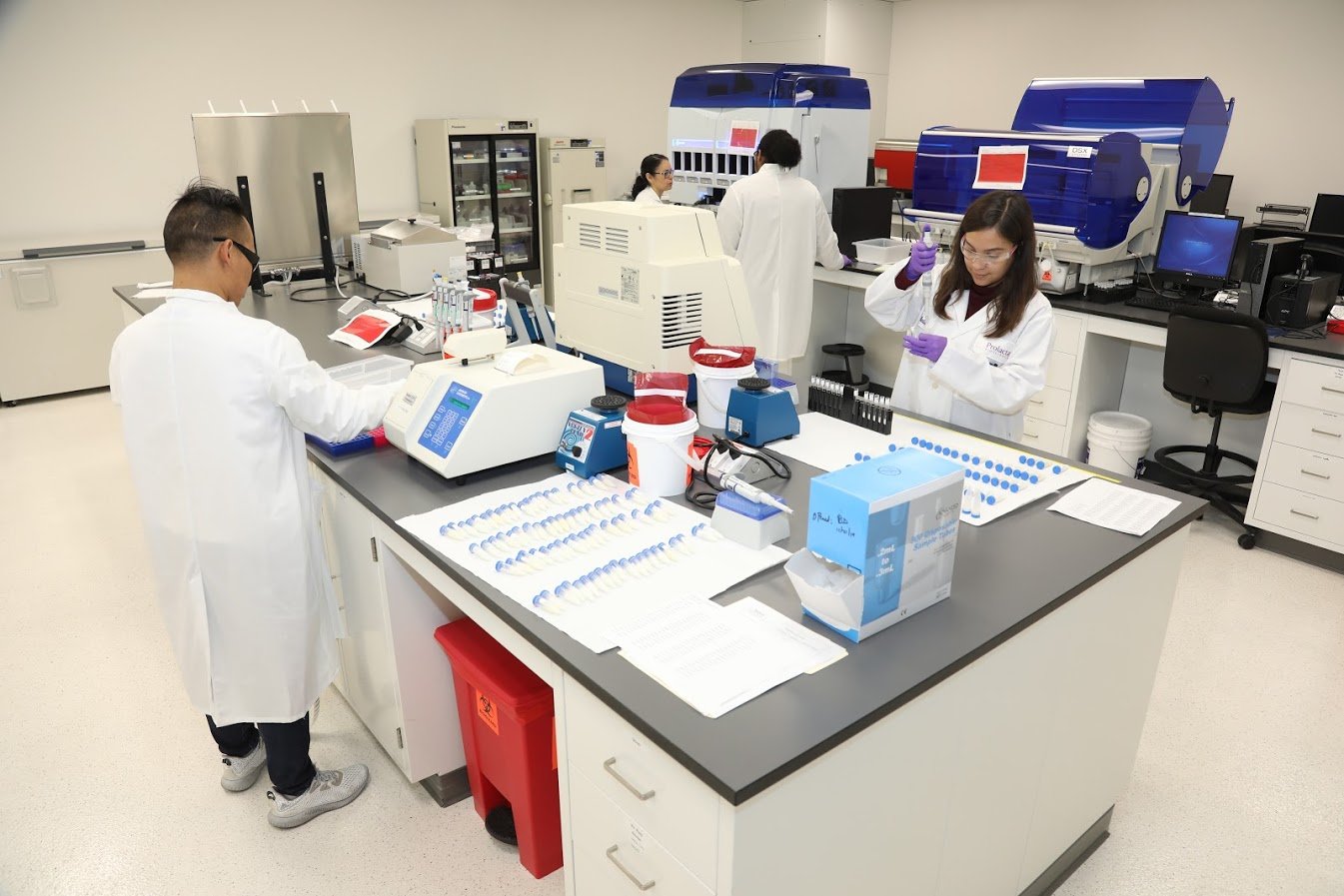
Pasteurised, quality and safety-assured
All of our nutritional products are pasteurised to ensure the highest quality and safety, using time and temperature profiles defined by the U.S. FDA in its Pasteurised Milk Ordinance (PMO) to destroy pathogenic viruses and bacteria. While there are other pasteurisation and sterilisation processes used in the human milk banking industry, only products manufactured with our pasteurisation